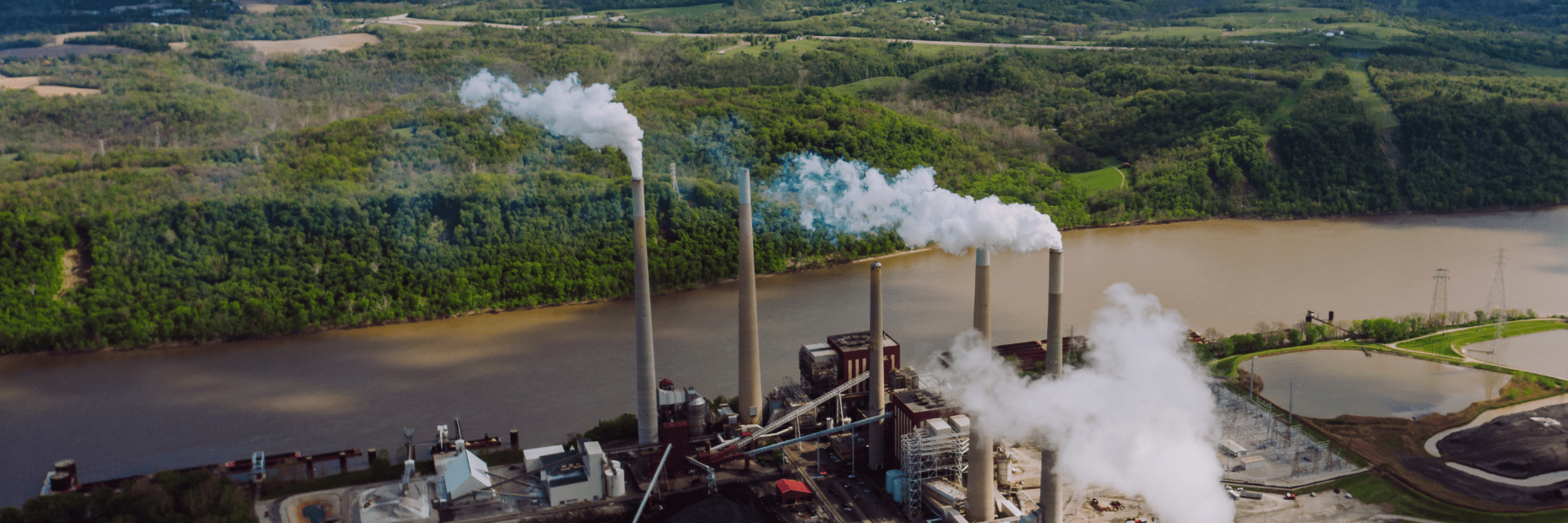
HOW CAN THE DIGITAL TWIN IMPROVE SUSTAINABILITY?
The digital twin is a virtual representation of a physical plant, process, or system created by integrating real-time data, simulations, and analytics. This virtual representation enables companies to monitor, analyze and optimize the performance of their assets in a virtual environment.
To help you better understand the power of the digital twin in the area of sustainability, we have created two graphs comparing processes of a factory with and without a digital twin. Take a look:
WITHOUT DIGITAL TWIN
In a traditional manufacturing environment without a digital twin, product-specific data is stored separately, leading to inefficiencies. Printed data sheets, suboptimal packaging, and limited traceability lead to waste and inefficiencies. In addition, customers do not have easy access to detailed product information, which impacts their experience.
WITH DIGITAL TWIN
The introduction of a digital twin makes the entire work process more efficient. Product-specific information is stored centrally, eliminating the need for printed data sheets. The use of a QR code enables easy access to product information and reduces the need for additional packaging material. This not only reduces waste, but also improves the overall work of employees.
It also enables real-time monitoring and analysis of a product’s lifecycle, valuable insights into resource consumption, and optimizes production efficiency and waste generation.
BENEFITS
The comparison between a factory without a digital twin and one with a digital twin clearly demonstrates the transformative power of this technology. With its ability to optimize processes, minimize waste, and enhance customer experiences, digital twin technology is aiming to revolutionize the way manufacturing companies operate, promoting a more sustainable and environmentally conscious future.